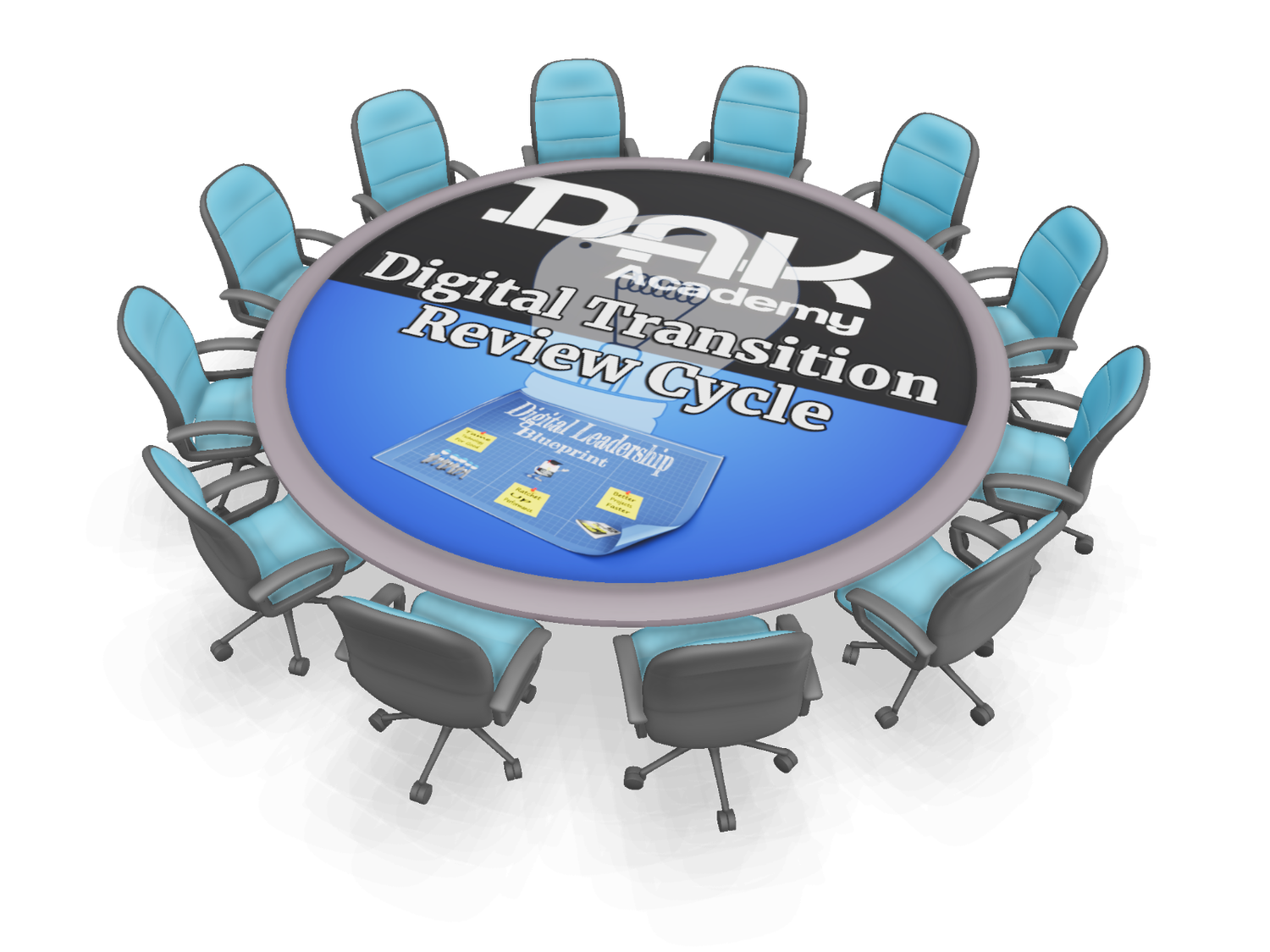
- Details
- Category: Blog
The fundamentals of how to ratchet up manufacturing effectiveness haven't changed. It's still a voyage of discovery with front line workers in the engine room. Their collective skills and experience are essential to counter the causes of waste and hidden losses by systematic improvement of basic conditions, standardised work routines and process control.
What has changed is a greater availability of real time data which enables better quality feedback and closer collaboration between production, maintenance and support functions.
Turning that potential into business gains is the equivalent of switching from letter post to emails or newspapers to smartphone news apps where the need for the post room or trip to the newsagent has disappeared. Something that requires collective leadership and a managed transition.
Those that do this well adopt a "Start Small, Learn Fast" approach using a series of small steps adding details as the learn more about what is possible, what works and how to use that to deliver business gains.
The time frame for these small steps is a quarterly cycle. This creates a transition cadence that is long enough to consolidate the working horizons of Senior leaders, Front Line Leaders and their teams as they apply and adapt to insights gained from using the Digital Ecosystem.
Digital Accelerator Training Workshops
The starting point for each cycle involves bringing together the right people in a working session to understand the current status, identify gaps and opportunities and develop shared action plans. TPM, Lean Maintenance and Make TPM Lean and Digital 3 day Accelerator workshops provide the vehicle to do that. (The choice of workshop content depends on the nature of the process involved.)
- During the workshop 0 to 15 participants work in teams of 5 on live assets or processes to:
- Define the scope out the are under review, assess criticality profiles, prioritise the trouble map issues and define a measurable improvement glide path
- Carry out a visual condition appraisal of plant and current work routines to identify refurbishment and skill development priorities.
- Assess how the digital ecosystem can be used to drive new thinking. That includes:
- Performance drivers: Review and action processes, Compliance feedback, Troubleshooting and Performance tracking.
- Cultural drivers: Engagement, Work planning, Standard setting.
The practical deliverables from the workshop include an agreed leadership agenda covering:
- Long term business deliverables,
- Measurable goals and a road map to progress towards that over the next 12 months,
- Detailed plans for the next quarterly cycle.
The intangible gains include:
- Increased understanding of functional perspectives and problem hot spots,
- An agreed vision and pressure for change,
- Creation of a network of likeminded change agents spanning organisational levels to deliver the change
The Quarterly Cycle
Following the mobilisation working session, the participants work in cross functional teams to progress action plans and integrate them within the day to day work routine. As well as adding detail to their plans, with coaching support, the projects become part of a collective learning experience.
Senior Leaders, Local Leaders and their teams learn how to make better use of data, how to share lessons learned and how to make use of new features such as personal dashboards, notification triggers and over the shoulder support.
These practical activities fuel their curiosity about what is possible resulting in "Use Case" proposals for simple smart apps to deal with problem hot spots or deliver improvement gains.
Typically Month 1 involves actions to:
- Awareness sessions to engage others in the forward work programme.
- Integration of forward plans into the day to day management process to:
- Improve and sustain asset condition,
- Enhance working practices and deal with skill gaps,
- Link up systems and make better use of available data:
- The aim is to build on existing systems and processes and provide the opportunity to define/test out/refine digital "Use Cases" in priority areas. Once approved the implementation of the enhanced digital ecosystem is used to support changes in work routines.
The detailed programme will vary for each organisation but includes milestones providing programme governance touchpoints at:
- Month 2: A short mid cycle review event to confirm that the improvement team has been mobilised and they are tracking the impact of their programme.
- At this point, the core teams will have identified issues and begun to apply countermeasures. In addition to specific improvements, this adds details to the leadership agenda in terms of standards to be enhanced and barriers to progress to be resolved.
- Month 3: A feedback event to summarise progress made, share insights and set out next steps.
- That includes the development of standards to transfer best practice, case study summaries to raise awareness and recognition to reinforce engagement with the change process.
- Preparation for the feedback event provides the opportunity for each team to take stock, reflect on progress, summarise lessons learned and develop plans for next steps. This is an important vehicle for engagement and the development of team and leadership capabilities.
The feedback is also the kick off session for the next quarterly improvement cycle.
Contact us for further details of how our TPM, Lean Maintenance or Make TPM Lean and Digital Accelerator workshops can be part of your systematic Improvement Process.