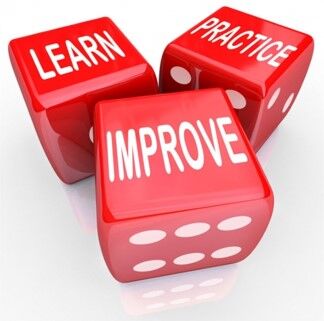
- Details
- Category: Resources
The Manufacturing Leader role involves problem solving to meet today's deadlines whilst simultaneously driving actions to improve future performance.
To do that well requires a sound understanding of:
- The causes of unplanned downtime, lost performance and quality defects,
- How to recognise and reduce accelerated wear,
- How to engage their team in activities to surface and prevent mis operation and wasted effort,
- How to turn a Plan, Do, Check Action cycle as part of the work routine.
The Learning Goals below set out a learning plan for Manufacturing Leader Core, Intermediate and Advanced skill levels to support their development.
When combined with practical improvement projects the coaching modules are used to provide demonstrated competence before progressing to the next level.
That provides Manufacturing Leaders with a common set of learning steps which directly impact on the performance of the operation.
Learning Plan: Core Level Competency
Learning Goals |
Module Title |
Understanding equipment performance, effective problem prevention and how to lock in the gains. |
FI1. Focussed Improvement concepts |
Understanding the causes and countermeasures to waste and hidden losses. |
C9. Targeting waste and hidden losses |
Setting equipment condition standards and reducing the causes of accelerated wear. |
C5, Learning from sporadic losses |
Analysing stoppages and developing effective countermeasures |
C6, Problem observation and root cause analysis |
Best practice procedure design and implementation |
C7. Improving demonstrated capability. |
Accelerated learning and problem prevention |
C8. Visual Management, single point lessons and learning plans |
Deliviring 90 day Focussed Improvement Cycles. |
CI1. Action planning |
Learning Plan Topics: Intermediate Level Competency
Learning Goals |
Module Title |
Understanding the steps to raise asset performance |
FI2. Focussed Improvement concepts |
Reduce idling and non value added activities |
I12. Improving workflow |
Enhancing work instructions and shared learning |
I9. Standardisation |
Improving set up and adjustment routines |
I11. Centerlining |
Setting standards to spot defects at a glance (so they don’t happen) |
II6. Enhanced Inspection Routines |
Transitioning from preventing downtime to preventing defects |
I8. Reducing unplanned intervention |
Reducing accelerated wear and the causes of failures. |
I10. Asset care |
Establishing best practice routines to improve process consistency |
I7. Setting and Sustaining Normal conditions |
Learning Plan Topics: Advanced Level Competency
Learning Goals |
Module Title |
Understanding equipment mechanisms and how to target the causes of defects and design weaknesses. |
FI3. Focussed Improvement concepts |
Managing progress from stabilise to optimise |
C9. Targeting waste and hidden losses, |
Defining necessary, desirable conditions. Incorporates applied Quality Maintenance and 6 Sigma application tools. |
S4. Foundations for optimal conditions |
Dealing with speed losses and process/product variability. |
S5. Targeting minor quality defects |
Improving problem detection and progress towards optimum conditions |
S6. P-M Analysis and Six Sigma |
How DAK Academy Can Help
The above coaching modules are designed to develop Manufacturing Leader ability to lead their teams through the improvement journey steps of:
- Breaking out of reactive
- Scaling up production
- Reducing Minor Stops and Quality Defects
- Delivering step out performance
Contact us for more information here