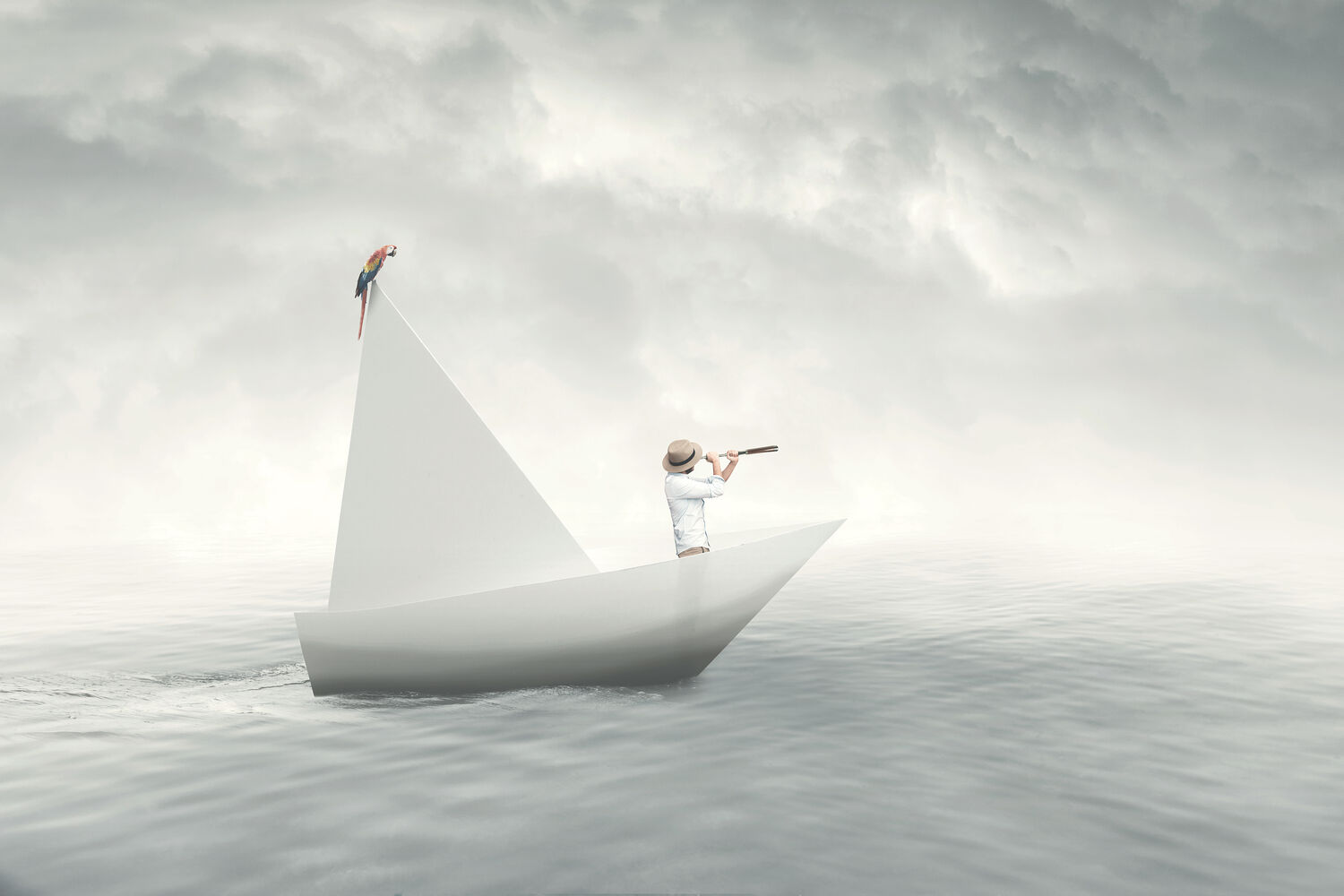
- Details
- Category: Resources
Although problem solving skills are desirable, an over dependence on them is a common characteristic of under performing organisations, Waiting for problems to occur before taking action, is a recipe for high costs and poor customer service.
Research into the causes of unplanned stoppages highlights how around 85% of unplanned downtime is due to human error and poor working routines. Investing time in Focussed improvement deals with these issues to achieve problem prevention rather than problem solving.
That is why organisations that deliver industry leading levels of performance embrace Focussed improvement as part of the daily routine. The outcome is a more reliable and resilient operation. As important is the way the approach encourages shared learning to lock in the gains, develop new capabilities and ratchet up performance.
This is an approach that delivers improvement pull from those nearest to the added value processes by:
- Establishing basic conditions, removing skill gaps and reducing waste/hidden losses.
- Progressing from silo thinking to cross functional collaboration to raise standards
- As recurring problems are resolved, routine tasks can be standardised and simplified to remove causes of human error and related quality defects.
- That improves flexibility and releases skilled resources to optimise process capability and ratchet up performance.
- Using time saved from dealing with unplanned downtime to support focussed improvement projects that:
- Increase mean time between intervention, improve material yield, reduce resource usage and identify opportunities to increase customer value.
- Develop high performance teams that can manage routine tasks and end to end supply chain coordination.
Planning the Plan
Begin with a planning the plan working session involving leadership/area project teams to:
- Raise awareness of improvement leadership best practice steps.
- Identify current status and future goals
- Agree areas of strengths and barriers to progress.
- Identify priorities and next steps.
As part of this, consider common causes of recurring problems such as:
- Knowledge and insight to sustain performance glide paths
- Weak or missing standard operating procedures and skill development processes
- Performance management processes
- Engagement with actions to deliver year on year performance gains
Aim to create a realistic and achievable 12 month programme in outline and an initial 90 day programme in detail covering:
- the 90 day project brief.
- the roles and personnel to be involved
- The potential gains.
- Timetable for the mobilisation phase.
The Quarterly Focussed Improvement Process
Below at Figure 1 is an outline process flow for a front line improvement team engaged with Focussed improvement alongside their daily duties over a quarterly cycle.
Figure 1 Workplace Learning Programme Overview
This includes short weekly meetings to communicate progress and coordinate action plans. The team will need some time outside of the meetings to gain an insight into cause/effect and test out ideas in the real world. The nature of that time depends on the project but expect any time used to deliver an annual return on that investment of 4 to 6 times. (Otherwise why do it?)
The focussed improvement process provides a cadence for leadership using timetabled coaching touchpoints to guide the Focussed improvement activity as part of the performance management routine.
These coaching touch points:
- Provide a forum for improvement team, front line and senior Leaders to reflect on progress made, agree actions in light of lessons learned and remove barriers to progress
- Inject training and specialist support as required
- Capture and transfer lessons learned.
How DAK Academy Can Help
Our support pathways can provide a mix of face to face, remote and customised on demand micro learning video’s and courses to develop in house capability to:
- Define problem scope and fix the real issues.
- Overcome inertia to change.
- Lock in the gains.
- Deliver improvement as part of the daily routine.
Support pathways provide a blend of training courses and coaching plans to meet the challenge of specific improvement agendas such:
Click on the links for more information or Contact us for more details of how we can help to develop your improvement capabilities.