Research for the book "Lean TPM a blueprint for change" plus our work with the UK Best Factories award programme led to the creation of a benchmarks database setting out the improvement journeys of over 300 organisations.
That provided an insight into what it takes to deliver lasting improvement as well as the common barriers to improvement progress.
This graphic below plots a typical improvement journey using the three improvement dimensions of plant, procedures and people in order of priority. For those organisations without large items of plant replace the term plant with operations or execution.
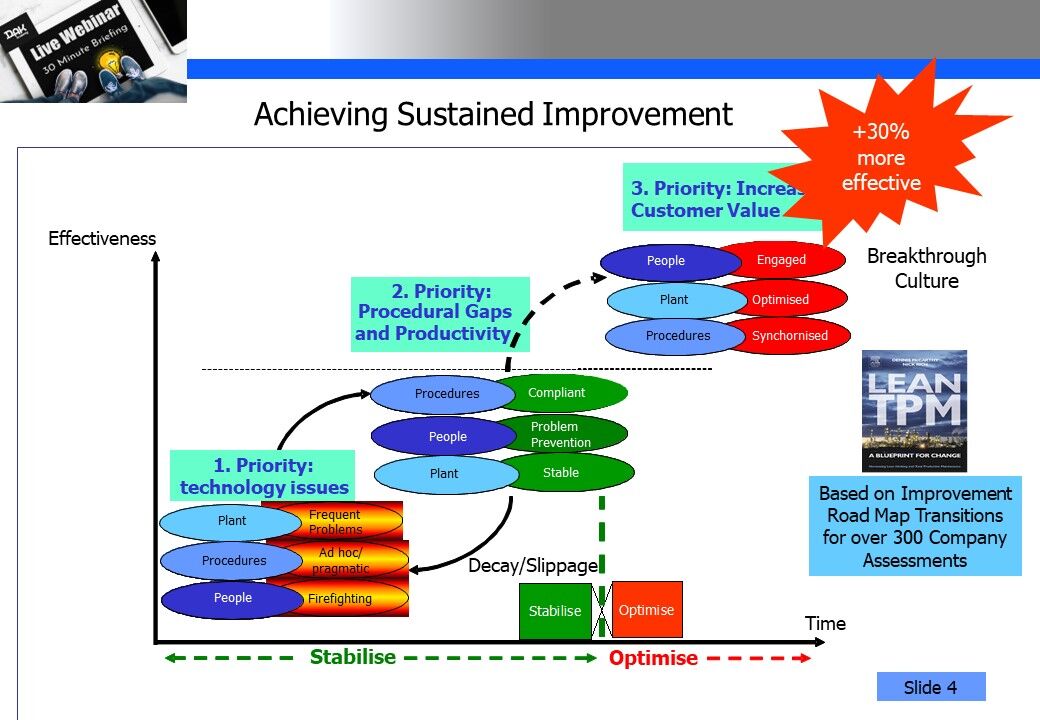
At the beginning of the journey the priority is plant or operations reliability with the goal of breaking out of reactive firefighting. The breakthrough to stable operations/zero breakdowns involves a focus on formalising procedures to establish basic asset conditions, reduce accelerated wear and waste. That improves effectiveness the flow of added value and saves time.
This approach can deliver significant gains but those who stop here find that the pace of improvement is not easy to sustain. As people move, new people join or new leaders take over, practices become diluted leading to decay and slippage or increased bureaucracy as organisations try and recover the situation. Creating a glass ceiling.
Organisations that are able to break through the glass ceiling sustain the gains by putting people and culture at the top of their improvement priorities. That creates improvement pull to support a step out outlook of growth by delivering new value to customers.
The evidence is that adopting the people development priority at any stage of the journey accelerates the pace of improvement and makes it easier to sustain the gains.