Better Project Delivery
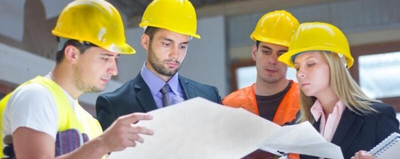
These training courses are for those meeting the challenge of specifying and managing projects to achieve flawless operation from day one. That includes how to meet individual project needs and where to enhance existing project management processes to deliver better projects faster.
Early Equipment Management
- Details
- Parent Category: Courses
- Category: Better Project Delivery
- Dates: Half day awareness
- Location: On line, In company
- Cost: £500 plus VAT (up to 8 delegates)
Early Equipment Management (EEM) was developed by leading organisations based on the lessons learned from projects that failed to achieve their expected cost, timeline or return on investment results due to unexpected but avoidable problems.
This 4 hour online live awareness session provides an insight into why Early Equipment Management delivers better projects faster and what it takes to do that.
- Learn how Early Equipment Management (EEM) delivers better projects faster
- Understand the EEM road map and glide path to flawless operation.
- Know how to apply the EEM road map to enhance project value and return on investment.
- Be able to transfer lessons learned during the course to in house projects.
-
Why Attend the workshop?
The workshop provides practical tools to enhance existing Project Governance and project delivery processes. This complements other project delivery tools such as Prince2, Design Thinking, Lean Design, 3P and 6 Sigma Design.
The learning goals for the workshop are to:
- Learn about Early Equipment Management (EEM) principles and how to apply best practice to future projects
- Understand the EEM road map and glide path to flawless operation.
- Know how to apply the EEM road map to enhance project value
- Be able to transfer lessons learned during the course to their next project.
The workshop will include theory, case studies, exercises to reinforce learning points and develop proposals to enhance current practices.
The workshop covers core competency learning contednt for the DAK Academy EEM Skills Passport.
Workshop Agenda- Introduction to workshop
- Agenda and Learning Goals
- The EEM Roadmap to Flawless Operation
- What goes wrong.
- The countermeasures
- The EEM road map
- Project Governance
- Getting the Right Design (Fixing the right issues)
- Common project management weaknesses and how to avoid them.
- Operations review
- Setting the project scope (Action Mapping)
- Applying EEM benchmarks to High Level Design Decisions
- Getting the Design Right
- Project organisation.
- Comparing options and selecting vendors.
- Ease of use and Maintenance Prevention
- Design to Life Cycle Cost to enhance project value
- Managing Project Delivery
- Designing the project glide path and witnessed inspection
- Installation and commissioning work packet design.
- Aligning multiple work streams.
- Troubleshooting and preparation for day 1 handover.
- Managing Operational Change
- Factory readiness challenges.
- Engaging local stakeholders with factory readiness plans.
- Integrating Installation, commissioning, with factory readiness plans.
- Ramping up production.
- Project Leadership
- Setting expectations and project goals
- Developing local area capabilities
- Becoming self sufficient.
- Site Acceptance Testing.
- Action Planning
- Assessing current capital project management processes.
- Implementing improved project delivery processes.
- 90 day action plan.
Workshop Leader ProfileDennis McCarthy- DAK Consulting
Dennis has supported Total Productive Maintenance, Lean Thinking and Continuous improvement programmes ranging in size from small single site applications to companywide multi-site transformation programmes in Europe, USA, India and China. This has included support for well-respected and award winning companies such as 3M, Ford, General Motors, GE, RHM and Dow Corning.
He is the author of 4 books on continuous improvement using Lean and TPM principles and Techniques. The course content is based on his most recent book, “Early Equipment Management, Continuous Improvement for Projects” published by Productivity Press. Within this are case study examples from his work helping well know and award winning organisations to deliver flawless operation from day one from capital projects. That includes Heineken, Ikea, Johnson Matthey, Mitsubishi and Rolls Royce Aerospace
Manufacturing Project Management Training
- Details
- Parent Category: Courses
- Category: Better Project Delivery
- Dates: 3 day training workshop
- Location: In Company Course
- Cost: £4500 up to 10 Delegates
Successful delivery of Manufacturing Projects depends as much on engaging stakeholders with new thinking and knowledge capture as it does on classic project management tools.
In addition, a significant proportion of the gains from smart technology are delivered by using the connectivity of the new technology to surface and deliver opportunities to improve management processes. In some cases it can also be the trigger to change the business model to access new markets and added value.
Investing in project manager and project team training, is not just a smart decision—it is essential for long-term success.
Learn how to avoid common manufacturing project pitfalls, deliver better value and achieve higher return on investment. Be able to develop a robust project management skill set.
Reasons why delegates booked a place on previous courses
-
Overview
Unlike generic Project Management processes created to manage contractual arrangements, this course is designed to meet the needs of Manufacturing Project Management. That involves projects where success depends on using tools to tap into internal tacit knowledge, facilitate decision making, coordinate the part time involvement of internal resources and engage people with changing ways of working.
That includes projects generated by Focused Improvement, new product introduction, Kaizen activities, layout changes, maintenance shut downs, capital projects, IT system implementations or changes to business processes.
These are projects where in addition to traditional planning, organisation and control of tasks, the project manager needs to guide and coordinate those in project and operational roles as the project progresses through the stages of design, development and delivery.
Nowhere is that more important than with Industry 4.0 projects which involves steps to
1. Develop "Use Case" concepts to match digital solutions to operational pain points
2. Implement successful use cases on a pilot basis to prove the approach and develop policy guidelines to support the transfer of the approach at scale to other parts of the organisation
3. Transfer the successful pilot approach to other parts of the organisation.Course content includes a mix of theory, case studies and practical exercises to provide experience of applying Project Management Processes that
- Facilitate cross functional collaboration and engagement of those involved in today's operations with the future success of the project to deliver buy in and support for change
- Encourage knowledge sharing, timely release of resources and effective decision making to deliver better solutions
- Coordinate the transition from "current to new" in a way that minimises the impact on customer service levels and delivers faster operational gains.
Course learning goals are to:
- Understand practical project management principles and techniques
- Know how to take a structured approach to project definition, justification and delivery
- Learn how to lead and guide project teams in a way that supports user engagement
- Be able to manage activities throughout the project life cycle from concept to delivery of beneficial operation.
Who is the course for?The workshop content is designed to help for those who have been tasked with delivering operational improvement. It is also relevant for Managers, Process Engineers and Change Agents, Team Leaders and Maintenance Engineers.
Course AgendaDAY 1
Introduction
Developing the project plan
• Confirming the scope, Developing the quality plan and task lists
• Defining the team and resource profiles, Developing the timetable
• Mobilising the project, Managing risks, Managing progress
• Measuring results and learning from experienceManaging people and teams
• Working with multi discipline teams, Creating a practical team vision
• Encouraging Innovation and creativity (within limits)
• Using visual management (improving understanding, exploring options, coordinating resources, mapping out collaborative interactions
• Using software (portals, document management, timetables and resource management)
• Managing technical change managementDAY 2
Recap
Personal organisation
• Getting organised,
• Developing Project management standard work
• Managing time, knowing your time traps
• Keeping in touch
• Facilitating MeetingsKnowledge management
• Understanding success criteria
• Collating tacit knowledge as design standards to aid early decisions and option selection
• Testing/learning through the use of models
• Understanding life cycle costs
Working with vendors and partners
• Setting design goals for low life cycle cost
• Defining design modules
• Selecting vendors
• Creating a shared project vision with clear accountabilities
• Collaborating on design/sharing knowledge
• Teasing out design weaknesses
• Value engineering
• Defining the installation plan.DAY 3
Recap
Equipment commissioning
• Planning the commissioning activity
• Pre-commissioning including FAT, installation hand over and SAT
• Inspections and testing
• Managing the commissioning process
• Refining ways of working
• Managing the training process
• Assessing completion stages and completing Site Acceptance Testing
• Post commissioning
Learning from experience
• Capturing lessons
• Data Analysis and machine learning
• A3 process case study
Developing a practical 90-day action plan
• Developing a vision the team can get behind
• Defining a realistic and achievable 12-month outcome
• Delivering results
Review of the Workshop
• Benefits, Concerns, Q&AWorkshop LeaderThe workshop will be led by Dennis McCarthy-DAK Consulting
Dennis began his career as an Industrial Engineer and led a number of major Logistics projects. He progressed to European Project Manager for a US Multinational managing pan-European Manufacturing, Logistics and IT projects. As a consultant he has supported manufacturing improvement programmes ranging in size from small single site applications to company wide multi-site transformation programmes in Europe, USA, India and China. This has included support for well-respected and award winning companies such as 3M, Ford, General Motors, Heineken, Pepsi, Rolls Royce and IKEA.