Embracing Digital Technology
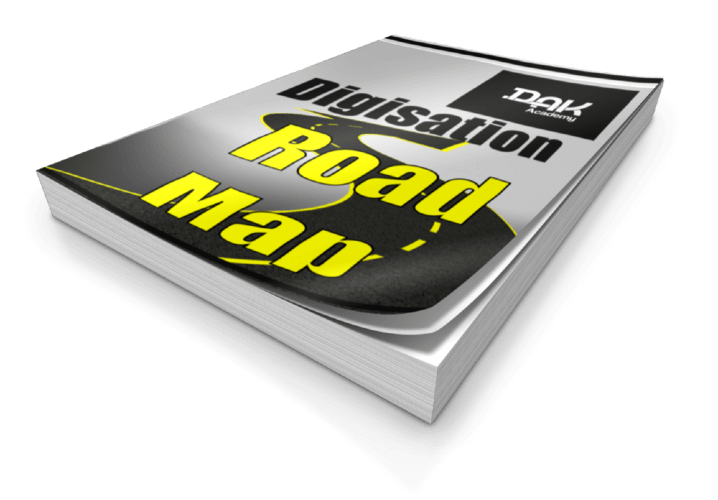
These training courses are for those meeting the challenge of delivering gains from Advanced Technology and Digitisation. That includes activities to surface and deal with the barriers to improvement from legacy rules of thumb and protocols.
Make TPM Lean and Digital 3 Day Course
- Details
- Parent Category: Courses
- Category: Embracing Digital Technology
- Dates: As required
- Location: In house course
- Cost: £4500 +VAT for up to 10 participants, £5000 for up to 15 participants.
In house 3 day training course.
Our comprehensive 3-day training workshop will accelerate your progress to implement Total Productive Manufacturing and Lean Thinking priciples using digital connectivity, feedback and analysis tools.
For Beginners:
- Learn how to apply the basics of TPM and Lean Thinking and use readily available digital platforms such as Microsoft Teams and SharePoint to accelerate the pace of improvement by linking up data from shop floor sensors and traditional IT systems.
For Advanced Participants:
- Discover how to blend digital strategies with TPM and Lean Roadmaps to take your existing Digitised Manufacturing Processes to the next level.
Book a course today to start your journey to Make TPM Lean and Digital.
-
Who should attend
This is a course for all those facing the challenge of adapting to the changing landscape of manufacturing in a digitised environment.
- Manufacturing improvement champions,
- Plant Managers,
- Team Leaders,
- Production supervisors,
- Maintenance Managers,
- Technicians,
- Engineers,
- Manufacturing Improvement Leaders.
What you will learnLearn
- What it takes to drive Total Productive Manufacturing (TPM) and Lean Thinking using our desktop OEE simulation.
Know
- How real time data analysis can improve insights into causal factors, speed up problem resolution to optimise the end to end plan, source, make deliver manufacturing process.
Understand
- Where Connected Worker and real time Dynamic Scheduling can deliver higher levels of reliability, accelerate the pace of continuous improvement and adapt to deliver gains from evolving technologies.
Be able to
- Develop a realistic and achievable plan to transfer lessons learned back to the workplace.
Course AgendaDay 1: Make TPM Lean and Digital Overview
- Introduction to TPM and Lean Thinking
- OEE (Overall Equipment Effectiveness) desk top simulation exercise
- The Smart Technology landscape, where the gains come from and how to adapt to advancing technology developments.
- The connected worker and systematic improvement:
- Loss Tree analysis/cost modelling,
- Dynamic Scheduling,
- Digital Twin glide path development.
Transfer to the selected production shop floor assets to perform a comprehensive assessment of manufacturing processes.
Work in small teams following a structured workbook with briefing notes covering:
Understanding the Asset
- Transactional Value Stream Map, Asset description and Criticality Assessment to collate operational knowledge re causal factors, performance drivers and reliability pain point,
- Definition of notification flags to sustain basic conditions and systematic improvement,
- Tracking true OEE levels and setting realistic and achievable 12 month improvement targets.
Day 2: Analysing Plant and Workflow Effectiveness Drivers
Delegates continue to work in small Teams on the shop floor projects covering:
- Condition Appraisal and Refurbishment Plan. This includes setting standards for basic conditions and the identification of accelerated wear.
- Development of a PFEA (Plan for every asset) covering Best practice asset care and correct operation. That includes identification of cross functional accountabilities and the integration of asset care with operating best practice.
- Standardisation covering:
- Work categorisation to reduce the risk of human error and enhance best practice compliance,
- Dynamic Scheduling and skill matching,
- Workplace organisation standards including local access to data.
- Learning plans
- to resolve skill gaps,
- Over the shoulder support,
- Team based capability development.
- The Connected Worker
- Creating a Digital Backbone,
- Data Management,
- Identification of analysis priorities, pain points and technology selection.
Day 3: Creating Digital Centres of Excellence
- Digital Ecosystem: Sustaining Basic Conditions
- Systemise "Normal Conditions" using condition based "Notifications" and trouble shooting algorithms plus over the shoulder support,
- Capture of lessons learned, sharing insights and accelerated scale-up.
- Digital Ecosystem: Systematic Improvement
- Data analytics as part of PDCA cycle to interpret data patterns, trends, and causal factors to Prevent unplanned downtime, extend component lifespan, optimise processes.
- Mini project feedback session
- Digital Ecosystem: Modelling and App Development
- Plan, Source, Make and Deliver process improvement.
- "Use Case" models and microservice applications to automate routines and support decision making,
- "Improvement Leader Networks" to engage the organisation with adopting smart technology.
- Developing Action Plans
- Transferring lessons learned on the course to the workplace.
Workshop LeaderThe workshop will be led by Dennis McCarthy.
Dennis has supported TPM, Lean Thinking and Continuous improvement programmes ranging in size from small single site applications to company-wide multi-site transformation programmes in Europe, USA, India and China. This includes support for well respected and award winning organisations such as 3M, Heineken, Pirelli and Rolls Royce. He has pioneered the use of Digitisation to accelerate the pace of improvement and the use of TPM and Lean roadmaps to guide the delivery of the gains from smart technology and digitisation.
Delivering Advanced Technology Gains
- Details
- Parent Category: Courses
- Category: Embracing Digital Technology
- Dates: 4 hour course
- Location: Live On Line Working Session
- Cost: £500 plus VAT (up to 8 delegates)
The lesson learned from successful early adopters of advanced technology is that that the biggest gains come not from the technology itself, but from the improved connectivity it provides. This can remove traditional communication delays between functions and with it uncertainty about what can be achieved. It can also provide rapid feedback to support the application of practical actions to improve workflows.
This half day on line session is designed to raise awareness of the evolving best practice road map for delivering advanced technology gains at scale (not just pockets of improvement). That includes
- The building blocks of success.
- How to avoid the common implementation pitfalls that result in pilot purgatory.
- How to engage the workforce with delivering disruptive gains from advanced technology.
-
Overview
Don't re invent the wheel. Use Lean and TPM principles and techniques to deliver gains from advanced technology. This short course provides an overview of how to do that and where to start.
It also includes activities to help you and your colleagues to identify barriers to progress and map out next steps to deal with them.
Successful adopters of advanced technology shown how this can deliver significant Quality, Cost and Delivery performance gains. In many cases this also releases new areas of customer value to raise the bar for customer expectations. Together, these gains have the potential to disrupt the business landscape making it harder for others to compete for customers and attract the best personnel.
While conventional wisdom might presume that delivering these gains requires a high levels of investment, leading organisations are achieving growth and higher productivity rates without the levels of costly investment which might have been required in the past.
The gains come from the improved connectivity provided by advanced technology. The outcomes include the creation of pragmatic workflows that accelerate gains from the use of Lean and TPM techniques to refine wasteful legacy work routines historically needed to deal with complex coordination of manufacturing resources.
The Digitisation of manufacturing management transforms the very nature of day-to-day operations by improving communications, allowing direct and indirect workers to focus on problem root cause identification and resolution.
At the heart of this programme is the engagement of cross functional improvement teams with clear objectives and effective collaborative working as part of the day to day operation. The enhanced connectivity also enables a closer integration of 3 improvement workflows into a Digital CI process to accelerate the delivery of gains from Lean and TPM principles and techniques.
Figure 1 Lean TPM Digital CI Process
In addition to the business gains, outcomes include higher employee engagement, focused training, skill development and improved problem solving capabilities.
Why Attend?Understand
- The advanced technology landscape, potential gains for your company and how to deliver them.
Know what it takes to
- Assess the gains from improved connectivity.
- Tap into the knowledge, skills and experience of the full company team.
- Engage them with the learning challenge and make them curious about the possibilities.
- Provide timely leadership to guide them towards the Quality, Cost and Customer service gains the business needs to prosper.
- Define your improvement road map milestones, identify who needs to be involved and plan the next steps of your journey.
Be able to
- Tame technology - by closing the gap between the technical and digital worlds
- Ratchet up improvement - through digitised resource management, Leading Indicators and Machine learning
- Enhance the speed and quality of skill development
- Adapt work processes
- Support rapid idea development and investment governance best practice
Who should attend?
The workshop content is designed for those faced with the challenge of tapping into the potential gains of advanced technology. That includes:
- Business Sponsors, key managers and team leaders
- Project Mangers
- Support personnel
- Manufacturing Engineers
- Change Agents and CI Facilitators
AgendaIntroduction
The Technology Landscape
- The advanced technology themes
- Where the gains come from
- Winning tactics and common pitfalls
Delivering the Gains
- Understanding connectivity
- Defining a problem finding process
- The Improvement Master Plan
Reliability
- End to End Value Stream
- Prioritising Improvement Areas
- Assessing Potential Gains
Workflow
- Process Review
- Work Management
- Standardisation
Daily Management
- System Infrastructure
- Real time task execution
- Workplace learning
Focussed Improvement
- Developing a Vision to Engage the Team
- Defining a realistic and achievable 12 month outcome
- Delivering results
Review of the Workshop
- Benefits, Concerns, Q&A
Led ByDennis McCarthy- DAK Consulting
Dennis began his career as an industrial engineer progressing into general management and director level roles. As a consultant he has helped well- respected and award winning organisations to accelerate the pace of improvement. This includes support for internal teams meeting challenges ranging from underperforming assets to company-wide multi-site transformation programmes in Europe, Australia, USA, India and China.